The 15″ MacBook Pro with Retina Display is by far the best computer I had ever used, no question about it. And I had used great many – although only a handful made a deep impression (I mean a positive impression, because I came across several that made unforgettable bad impressions). These are heavy words from me. As you might have been noticed I’m really picky on everything I use (just browse the Hall of Shame section for rants about bad design and/or execution).
You can read my initial impressions about the machine here.
During the last months I had used the machine as a desktop for software development (both iOS and OS X) as well as studio work, and lugged it around the country as a field laptop to assist during my photo trips. Most of my first impressions are still valid, and I love the machine even more than I though at first. I would just like to add further observations.
Battery Life
In my initial post I wrote around 5 hours. Since then OS X 10.8.2 came out, which increased battery life substantially. Now I get something between 6 and 8+ hours, depending on the usage pattern (disabling Adobe Flash holds a great contribution to increased battery life, though).
Tethered Shooting
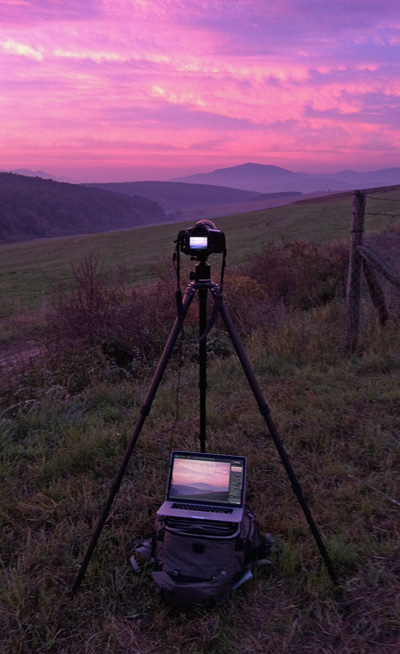
Working Tethered
I started working tethered for landscape shots immediately after receiving the MacBook, and the benefits far outweigh the inconvenience of lugging around a computer. Before the MacBook I had tried to use the Lenovo X200s for tethered work, but was not really satisfied with it and abandoned the idea until the MacBook arrived.
I like several things about this setup.
No time required for image sorting and selection later. I just bring home the keepers. This proved to be a huge time-saver!
I can make the first cut of the final processing in the field, using the same tools I use in the studio. This fits extremely well into my creative process. The high resolution and color-accurate display helps a lot in this. It’s like holding an A4 sized print in front of me. I even stitch panoramas made with the 24mm TS-E lens to check whether everything is good about the shot.
Images are immediately backed up, as the the tethering software saves images to both the memory card in the camera and onto the computer. (Which app? – you might ask. Don’t worry I’ll devote a few posts for that subject later.)
As I wrote in my first impressions piece, the machine fits perfectly into my Lowepro Pro Trekker 400AW. Fully loaded it’s now a back-breaking experience, but if I leave home stuff I don’t need for the shoot, then the full weight is around 15kg, which is bearable. I did several 2-3 hour hikes with the setup without any effects on my back and shoulders (did I mention that the Pro Trekker is a great backpack?).
Other Good Things
The notebook-as-the-desktop was really helpful during the August storms. I routinely power down and disconnect sensitive equipment during thunderstorms, as I saw quite a few over-voltage spikes in the past. But with the MacBook I can continue working during these hours. I really like thunderstorms and they put me in a creative mood, so it’s a big plus!
Last, but not least, no more copying or syncing or Dropboxing files between my desktop and field notebook! No more forgetting to copy something in the hurry before I leave! This saves me lot of time and the peace of mind that comes from the fact that I always have everything I need with me is priceless.
What I miss?
Thunderbolt docks. Matrox’s and Belkin’s solutions are both delayed. Plugging in all those cables (all the connectors of the machine are populated) in the morning really pisses me off. I’ll be first in the line for one of those docks!